Has anyone wondered what goes into creating the perfect soap? It’s not just about mixing ingredients; it’s an art and science combined, resulting in a product that cleanses, nourishes, and delights.
As an expert in the cosmetic industry, I bring a wealth of knowledge about the soap manufacturing process. My insights are based on industry experience and understanding of what makes a high-quality soap product.
The soap manufacturing process is a journey from raw materials to the final, fragrant bar. It’s a blend of careful ingredient selection, precise measurements, and creative craftsmanship.
In this guide, we will delve into the 9 essential steps of the soap manufacturing process. From sourcing the finest ingredients to the final packaging, each step is crucial in creating a product that stands out in the competitive skincare market.
Read on to unlock the secrets of successful soap making.
Step#1 Pre-Manufacturing Preparation
To begin the soap manufacturing process, careful pre-manufacturing preparation is essential. This stage sets the foundation for the quality and characteristics of the final product. Here’s how to do it:
- Selection of Raw Materials: Choosing the right raw materials is the foundational step. This includes selecting fats or oils, which impact the soap’s moisturizing properties, and alkalis like sodium hydroxide, crucial for saponification. High-quality materials are essential for a superior end product tailored to specific skincare needs.
- Quality Control of Ingredients: After selecting the raw materials, they undergo rigorous quality control. This step involves testing for purity, consistency, and safety, ensuring each ingredient adheres to industry standards. It’s vital for preventing contamination that could compromise the soap’s quality and safety.
- Formulation of the Soap Recipe: Formulating the soap recipe is a critical step. It involves determining precise ratios and combinations of ingredients to define the soap’s characteristics, such as hardness, lather, and moisturizing properties. Accurate formulation is key to achieving the desired product quality.
- Preparation of Equipment and Workspace: The last part of the preparation involves setting up manufacturing equipment and organizing the workspace. For example, cleaning and sterilizing tools and machinery, and ensuring all safety measures are in place. A well-prepared environment is crucial for a smooth and efficient manufacturing process.
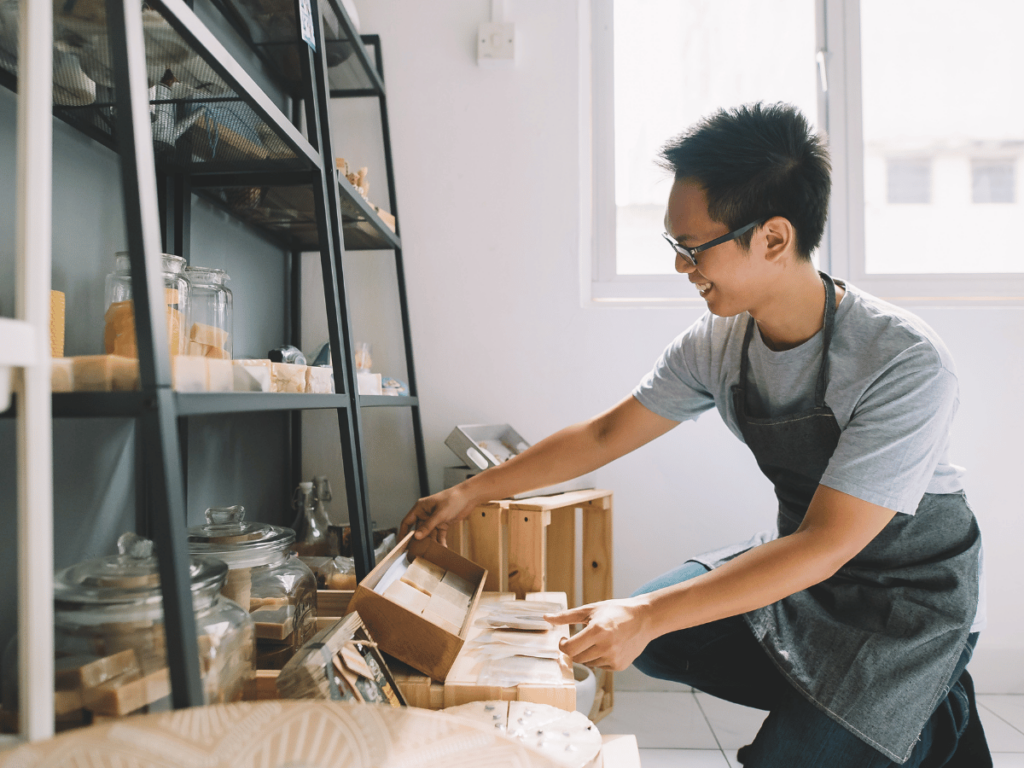
Step#2 The Saponification Process
Following the pre-manufacturing preparation, the next critical step is the saponification process, where the actual soap formation occurs. Below are the essential steps in this transformative process:
- Mixing Fats and Alkali: The process begins by mixing the selected fats or oils with an alkali, typically sodium hydroxide. This mixture is carefully heated to a specific temperature, facilitating the reaction. The accuracy of temperature and proportions is crucial for the success of this chemical reaction.
- Monitoring the Saponification Reaction: Once mixed, the saponification reaction starts. During this stage, it’s essential to continuously monitor the mixture for consistency and pH levels. The reaction is exothermic, releasing heat, which must be regulated to maintain a steady reaction rate.
- Reaching ‘Trace’: The ‘trace’ stage is a key milestone in saponification. It’s the point where the mixture thickens to a consistency similar to pudding, indicating that saponification is proceeding correctly.At this stage, any additional ingredients, such as fragrances or colorants, are added.
- Testing and Completing the Reaction: The final step in saponification involves testing the mixture for complete reaction. This can be done through pH testing or other chemical methods. Once the reaction is complete, the mixture transitions to the next stage of soap manufacturing, ensuring that the base soap is ready for further processing.
Step#3 Milling and Refining
After the saponification process, the soap mixture transitions into the milling and refining stage, which enhances its texture and consistency. Below are the steps to effectively do this phase:
- Cooling and Solidifying: Initially, the soap mixture needs to be cooled and allowed to solidify. This is often done in molds or frames where the soap can set uniformly. The cooling process is crucial as it determines the soap’s initial hardness and texture.
- Milling the Soap: Once solidified, the soap is passed through a milling machine. This machine grinds the soap into uniform, smooth particles. Milling helps to fully blend all the ingredients, ensuring a consistent texture throughout the soap. TY Cosmetic employs this milling process in their soap production to guarantee a uniformly smooth and high-quality product.
- Refining for Smoothness: The milled soap is then put through a refining process. This involves pressing the soap through fine screens or rollers to further smooth and homogenize the mixture. This step is essential for achieving the desired fineness and ensuring a premium feel.
- Removing Air and Moisture: The final part of this stage involves removing any trapped air and excess moisture from the soap. This is usually achieved through vacuum processing or other techniques. Removing air and moisture is vital for soap’s stability and longevity, preventing cracking and shrinkage.
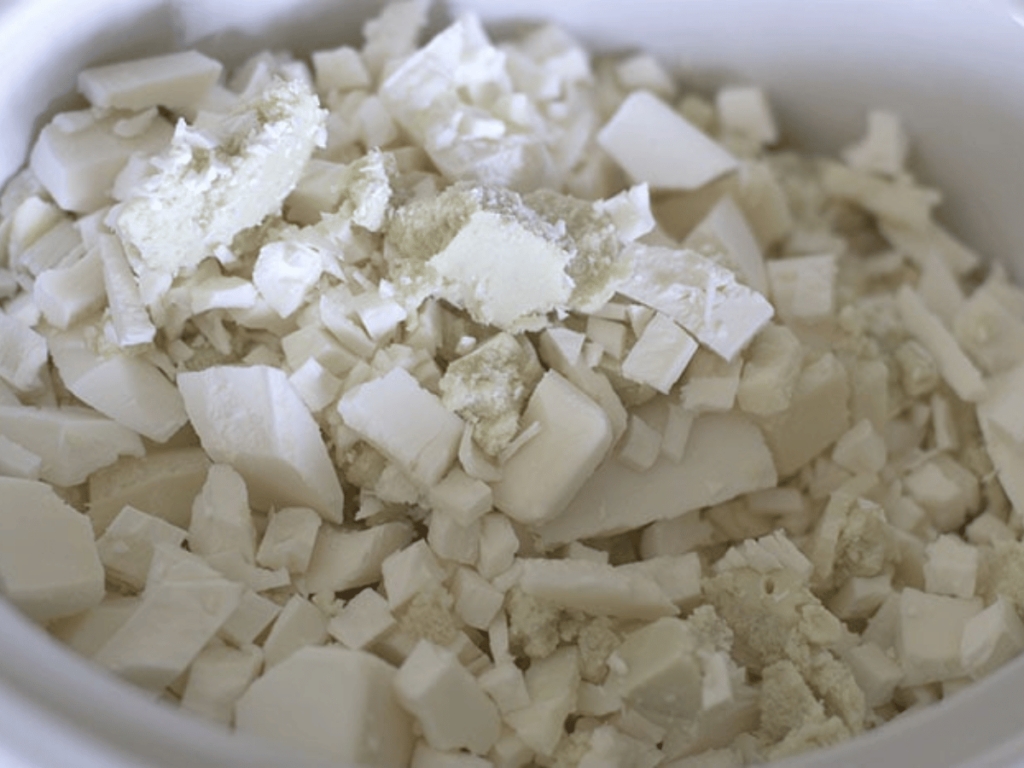
Step#4 Adding Fragrances and Additives
Following the milling and refining, the next phase involves the incorporation of fragrances and additives, which enhance the soap’s appeal and functionality. Here are the key steps in adding fragrances and additives:
- Selecting Fragrances: The choice of fragrance is a critical step. Fragrances can range from essential oils to synthetic perfumes, depending on the desired aroma and target market. It’s important to choose sensitive skin safe fragrances and align with the brand’s image.
- Incorporating Additives: Additives like moisturizers, exfoliants, or colorants are added to the soap to enhance its properties. These additives are carefully selected based on the soap’s intended use and the needs of the target audience. For example, glycerin may be added for extra moisturizing properties.
- Ensuring Even Distribution: Once the fragrances and additives are selected, they are thoroughly mixed into the soap base. This step is crucial to ensure an even distribution of these components throughout the soap, which is essential for consistent quality and performance.
- Testing for Allergens and Irritants: After adding fragrances and additives, these tests ensure the safety and suitability of soap for various skin types, particularly for products targeting sensitive skin. TY Cosmetic strictly tests their products at this stage to ensure they meet the highest standards of safety and comfort for all skin types.
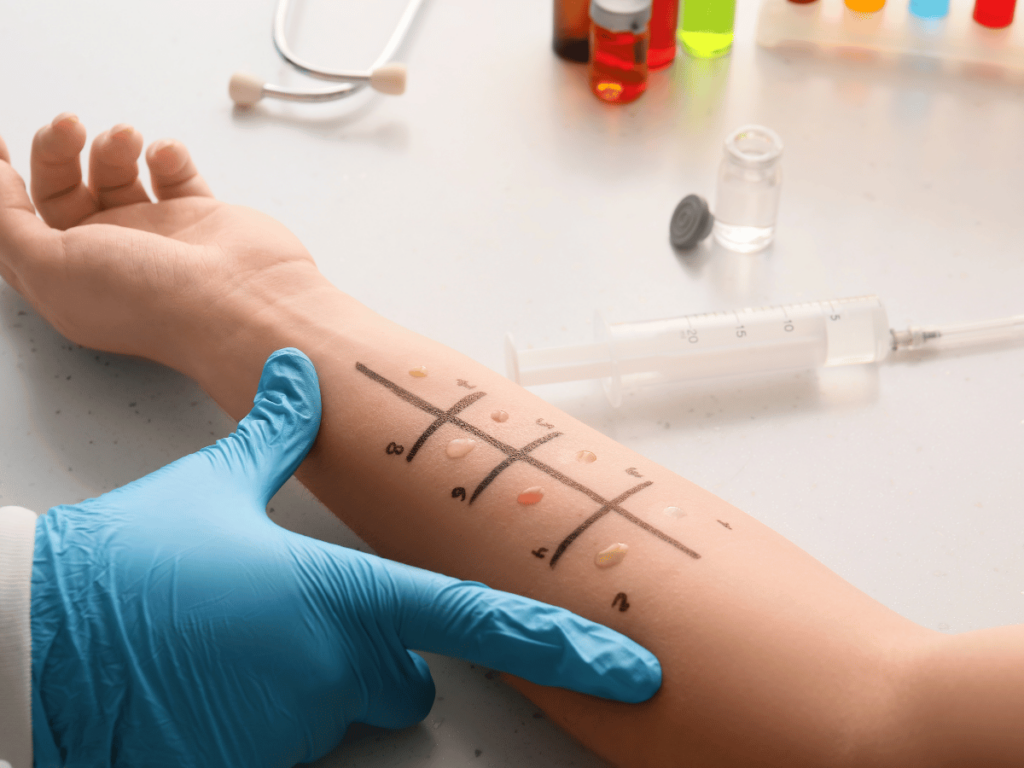
Step#5 Shaping and Molding
After the addition of fragrances and additives, the soap is ready for shaping and molding, a crucial step that gives the soap its final form and appearance. Below are the essential steps in this phase:
- Choosing Molds: The first task in this step is selecting appropriate molds for the soap. These molds can vary in shape, size, and material, such as plastic, silicone, or wood. The choice of mold depends on the desired final shape and size of the soap bars.
- Pouring the Soap Mixture: Once the molds are chosen, the soap mixture is poured into them. This is done carefully to avoid air pockets and ensure a smooth surface. The pouring process must be precise to maintain uniformity in size and shape across all soap bars.
- Cooling and Setting: After the soap is poured into molds, it needs to cool and set. This process can take several hours to days, depending on the soap composition and ambient conditions. Proper cooling is essential for the soap to harden correctly and maintain its shape.
- Unmolding and Inspection: Once the soap is set and hardened, it is removed from the molds. Each bar is then inspected for quality, including checking for imperfections or inconsistencies in shape and size. This quality control step ensures that only the best products reach the market.
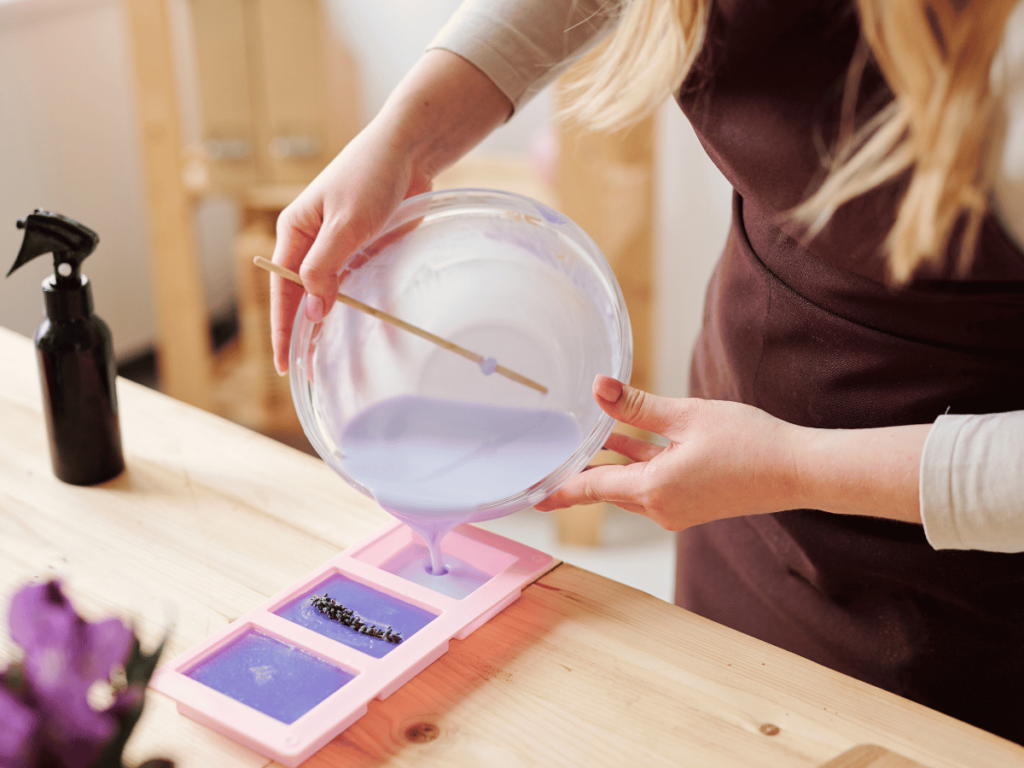
Step#6 Curing and Aging of Soap
Once the soap has been shaped and molded, it undergoes the crucial process of curing and aging, which significantly impacts its final quality. Here’s the detailed process that happens in this phase:
- Placing Soap in a Controlled Environment: The curing process begins by placing the soap in a controlled environment. This is typically a well-ventilated area with consistent temperature and humidity levels. The environment plays a critical role in ensuring the soap cures evenly and effectively.
- Duration of Curing: The curing period can vary, generally lasting from several weeks to months. During this time, the soap undergoes a slow evaporation process, which removes excess water and allows the soap to harden properly. The duration of curing depends on the soap’s formulation and desired properties.
- Monitoring Hardness and pH Levels: Throughout the curing process, it’s important to regularly check the soap’s hardness and pH levels. These factors are indicative of the soap’s readiness for use. A properly cured soap should be firm and have a balanced pH that is gentle on the skin.
- Aging for Enhanced Quality: Some soaps benefit from an additional aging process after curing. Aging can enhance the soap’s characteristics, such as its fragrance and leather quality. This step is especially common in artisanal and specialty soaps, where a longer aging process can add value to the final product.
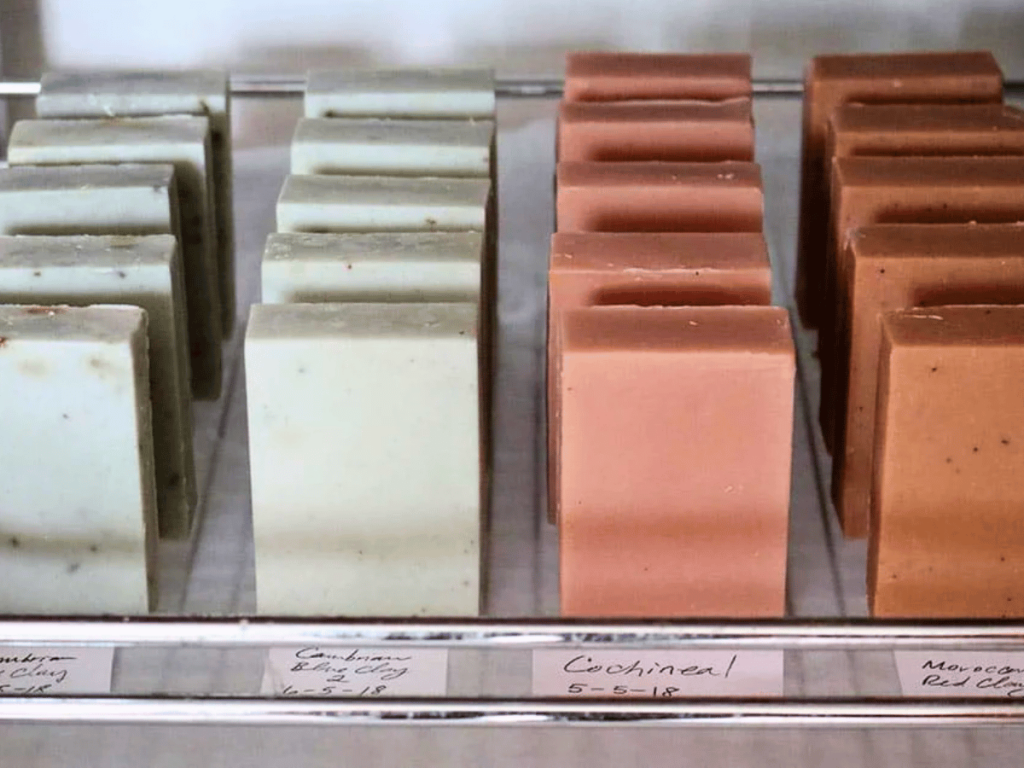
Step#7 Quality Control
Following the curing and aging process, the soap undergoes a critical phase of quality control to ensure that it meets industry standards and consumer expectations. Below are the main activities in this step:
- Visual Inspection: The first step in quality control is a visual inspection of the soap. This involves examining each bar for consistent color, size, shape, and absence of defects like cracks or air pockets. A uniform appearance is crucial for consumer appeal and brand consistency, especially in sectors like laundry liquid manufacturer where consistency signifies quality.
- Testing for pH Balance and Skin Irritation: Each batch of soap is tested for pH balance and potential skin irritation. This is done to ensure the soap is gentle and safe for use. A balanced pH, typically between 9 and 10 for soap, is essential for maintaining skin health and avoiding irritation.
- Performance Testing: Performance tests are conducted to assess the soap’s lathering ability, cleansing power, and how it reacts with water. These tests are crucial for verifying the soap’s functional quality and ensuring it meets the desired performance standards.
- Packaging and Label Accuracy: Finally, the soap is checked for accurate packaging and labeling. This includes verifying the correct listing of ingredients, usage instructions, and any claims made on the packaging. Accurate labeling is a key aspect of consumer trust and product transparency.
The table below focuses on the crucial role of packaging and label accuracy in soap manufacturing, underlining how precise and truthful labeling and packaging are essential for building consumer trust and ensuring product transparency.
Aspect of Packaging and Label Accuracy | Description | Impact on Consumer Trust and Compliance |
Accuracy in Ingredient Listing | Ensuring that all ingredients used in the soap are correctly and clearly listed on the packaging. | Enhances Transparency: Accurate ingredient listing is vital for consumer safety, particularly for those with allergies, and it enhances the overall transparency of the product. |
Correct Usage Instructions | Verification that usage instructions and any necessary precautions are clearly and accurately provided on the packaging. | Ensures Safe Use: Precise instructions help consumers use the product safely and effectively, which is crucial for maintaining consumer trust and product integrity. |
Claims Verification | Checking that any claims made on the packaging, such as ‘organic’, ‘natural’, or specific benefits, are truthful and substantiated. | Maintains Regulatory Compliance: Accurate labeling in terms of claims is essential for compliance with regulatory standards and avoids misleading consumers, thereby upholding brand credibility. |
Step#8 Packaging and Branding
After passing quality control, the soap is ready for the final stage of packaging and branding, which plays a significant role in market appeal and brand identity. Let’s explore how to effectively perform this phase:
- Design Attractive Packaging: The first step is to design packaging that is both attractive and functional. According to Manipal Digital, 60% of people make purchasing decisions based on product packaging. This highlights the need to choose materials that protect the soap and keep it fresh, while also considering environmental impact.
- Incorporate Brand Elements: Brand elements such as logos, color schemes, and unique design features are integrated into the packaging. This is crucial for brand recognition and differentiation in the market. Consistent branding across products helps in building brand loyalty and identity.
- Label with Essential Information: Labels are added to the packaging, containing essential information like ingredients, usage instructions, and any relevant certification.Accurate and clear labeling is not only a regulatory requirement but also key to consumer trust and satisfaction.
- Eco-Friendly Packaging Options: In response to growing environmental concerns, many brands are opting for eco-friendly packaging solutions. This could include biodegradable materials, minimal packaging, or recyclable components.Eco-friendly packaging resonates with environmentally conscious consumers and reflects a commitment to sustainability.
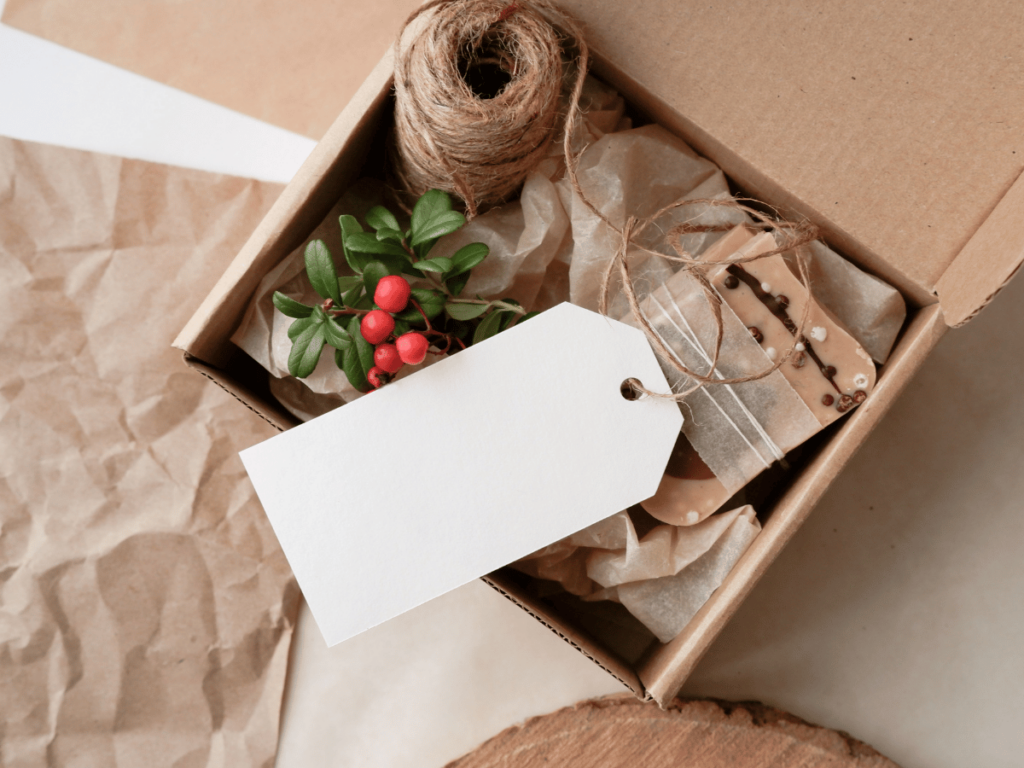
Step#9 Storage
This final step in the soap manufacturing process focuses on effectively storing the finished product to preserve its quality and integrity. Here are the steps involved in this phase:
- Choose Storage Facilities: The first step is selecting a storage facility that offers the right conditions for soap. This includes a cool, dry environment with stable temperatures and humidity levels. The facility should be clean and well-ventilated to prevent any buildup of moisture that could affect the soap.
- Implement Proper Shelving and Spacing: In the storage area, soaps should be placed on shelving that allows for air circulation around each product. Adequate spacing is important for products from bar soap manufacturers to prevent the transfer of scents between different soaps and to reduce the risk of any physical damage to the packaging or the soap itself.
- Monitor Environmental Conditions: Regular monitoring of environmental conditions such as temperature, humidity, and light exposure is crucial. Fluctuations in these conditions can adversely affect the soap’s quality, leading to issues like melting, fading, or the development of rancidity.
- Organize Retrieval and Distribution: Finally, the soap should be organized systematically, typically by batch number or date of production. This organization facilitates efficient retrieval for distribution, ensuring that products are shipped out in the order they were manufactured. It also helps in tracking inventory and managing stock levels effectively.
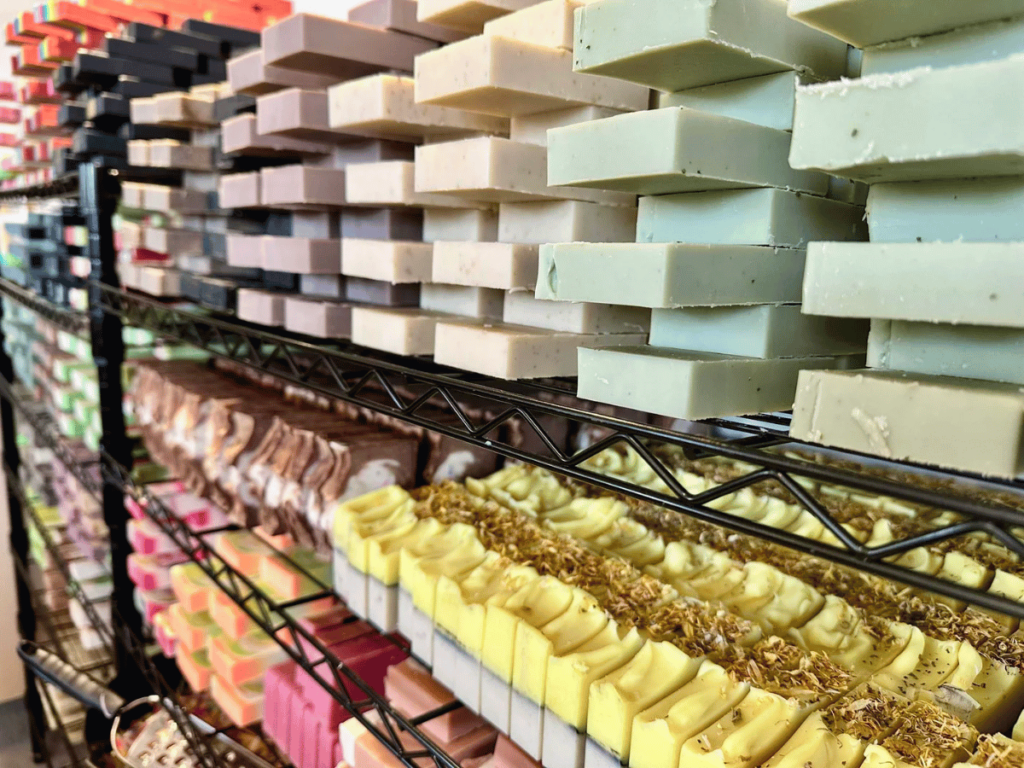
Dive Deeper Into Our Resources
Interested in discovering more? Gain instant access to our diverse range of products:
Still haven’t found what you’re looking for? Don’t hesitate to contact us. We’re available around the clock to assist you.
Conclusion
In conclusion, this comprehensive guide illuminates the intricate and fascinating steps involved in soap manufacturing, offering valuable insights for anyone in the industry. By understanding and implementing these steps, you can elevate the quality and appeal of your soap products.
If you’re looking to refine your soap manufacturing process or explore innovative formulations, TY Cosmetic is here to assist. To learn more or collaborate, feel free to contact us.