Have you ever wondered what goes into creating a laundry soap? The process is a fascinating blend of chemistry and engineering, resulting in a product that is an essential part of daily life.
As a laundry soap expert with years of experience in product formulation and manufacturing processes, I have a deep understanding of the intricate steps involved in creating effective and safe laundry soap.
The manufacturing of laundry soap is not just about mixing ingredients; it’s an art that balances science and technology to produce a product that is both effective and gentle on fabrics.
In this guide, we will explore the 10 essential steps behind laundry soap manufacturing. You will gain insights into the complexities of each stage, from ingredient selection to final packaging.
So, keep reading!
Step #1: Machine Preparation
The initial step in laundry soap manufacturing is machine preparation, a crucial phase that sets the stage for a smooth and efficient production process. Here’s what happens during this stage:
- Selection of Appropriate Equipment: The first task in machine preparation involves selecting the appropriate machinery for the soap-making process. This selection is based on the scale of production, type of soap being produced (bar, powder, liquid), and specific manufacturing requirements.
- Cleaning and Sterilization: Before beginning the production, it is essential to thoroughly clean and sterilize all equipment. This step is crucial to prevent contamination and ensure that the soap is hygienic and safe for use. Special attention is also given to parts of the machinery that come into direct contact with the soap ingredients and the final product.
- Calibration and Safety Checks: Once the equipment is clean and sterile, the next step is to calibrate the machinery and perform safety checks. Calibration ensures that the equipment operates within the required parameters, such as temperature, pressure, and mixing speed.
Step #2: Saponification Process
This step, employed by manufacturers like TY Cosmetic in laundry soap production, is pivotal in defining the soap’s quality and characteristics. Here’s an overview of the saponification process:
- Mixing Fats or Oils with Alkali: According to Thought Co., the process begins by mixing fats or oils with a strong alkali, typically sodium hydroxide (NaOH) for solid soaps or potassium hydroxide (KOH) for liquid soaps. The alkali is carefully measured to ensure the correct ratio for the saponification process.
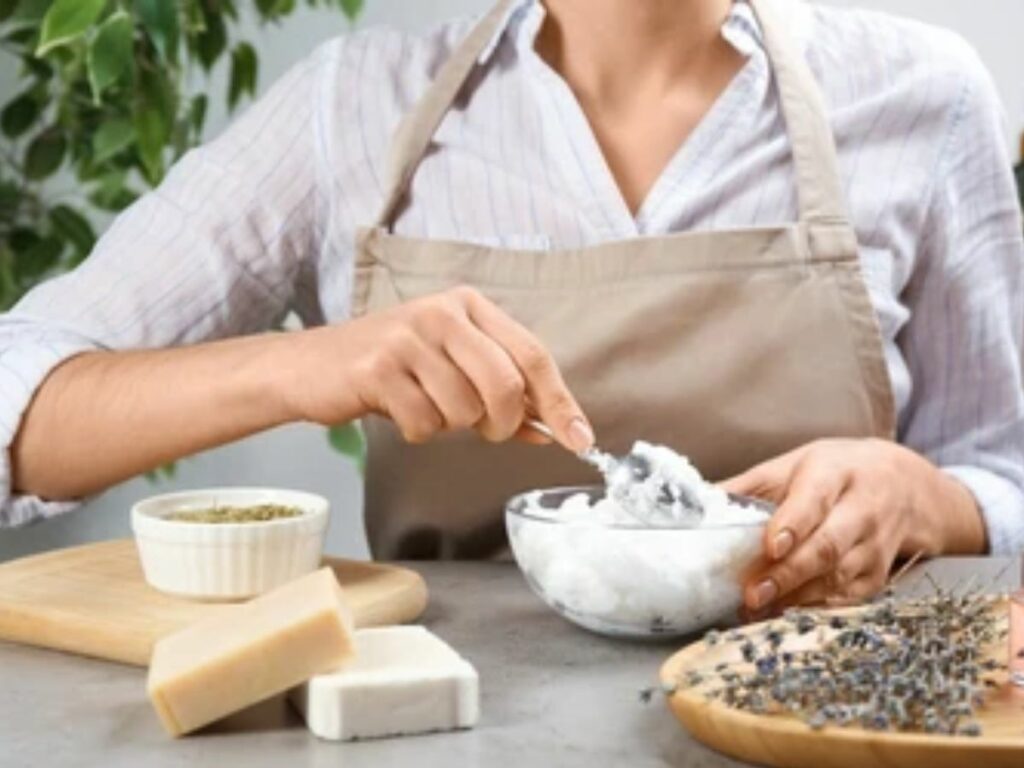
- Controlling Temperature and Mixing: Once the fats or oils and alkali are combined, the mixture is heated and stirred. The temperature and mixing speed are critical factors that need to be carefully controlled to ensure a consistent and complete reaction.
- Monitoring the Saponification Reaction: Throughout the process, the progress of the saponification reaction is closely monitored. This is done by checking the pH level of the mixture, ensuring that it reaches a level indicating the completion of the reaction.
- Neutralization: After saponification is complete, any excess alkali in the mixture is neutralized, often using a weak acid such as citric acid. This step is crucial to ensure that the final soap product is skin-friendly and not overly harsh.
Step #3: Soap Purification
After the saponification process, the next critical phase in laundry soap manufacturing is soap purification. Here are the key aspects of the soap purification process:
- Separation of Glycerin: One of the by-products of the saponification process is glycerin, which needs to be removed to enhance the soap’s cleaning efficacy. This is typically done through a process called glycerin separation, where glycerin is extracted due to its different solubility properties compared to soap. The removed glycerin is often used in other cosmetic products.
- Elimination of Excess Alkali and Unreacted Fats/Oils: Ensuring that no excess alkali or unreacted fats/oils remain in the soap is crucial for the safety and quality of the product. This is usually achieved through washing the soap with water, which helps to remove these impurities. The soap may go through several washes to ensure thorough purification.
- Soap Refining: The soap then undergoes a refining process, which can involve passing it through a series of rollers or using refining equipment designed to homogenize and smooth the soap mixture. This step is crucial to improve the texture and consistency of the soap, making it more uniform and free from any small particles or impurities.
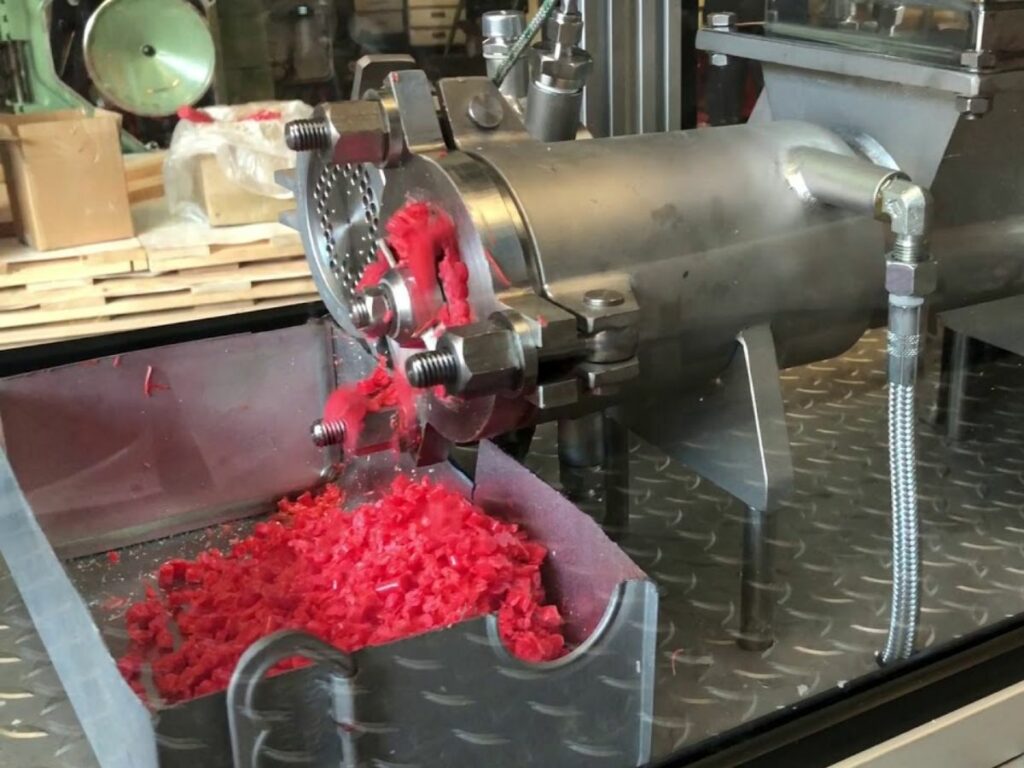
- Adjusting pH and Additives: The pH level of the soap is adjusted to ensure that it is skin-friendly and effective in cleaning. This might involve neutralizing any residual alkali. Additionally, any necessary additives, such as moisturizers or conditioners, can be incorporated during this stage to enhance the soap’s properties.
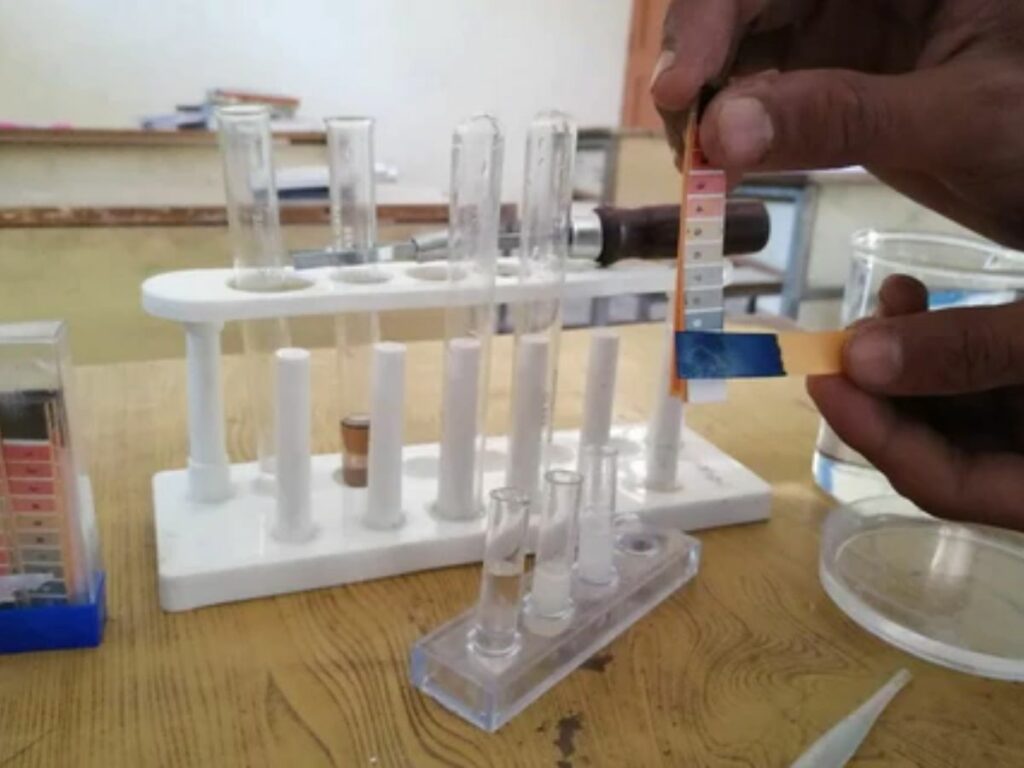
Step #4: Adding Fragrances and Colorants
At this stage in laundry soap manufacturing, the focus shifts to enhancing the sensory appeal of the soap through fragrances and colorants. Here’s how these elements are typically incorporated:
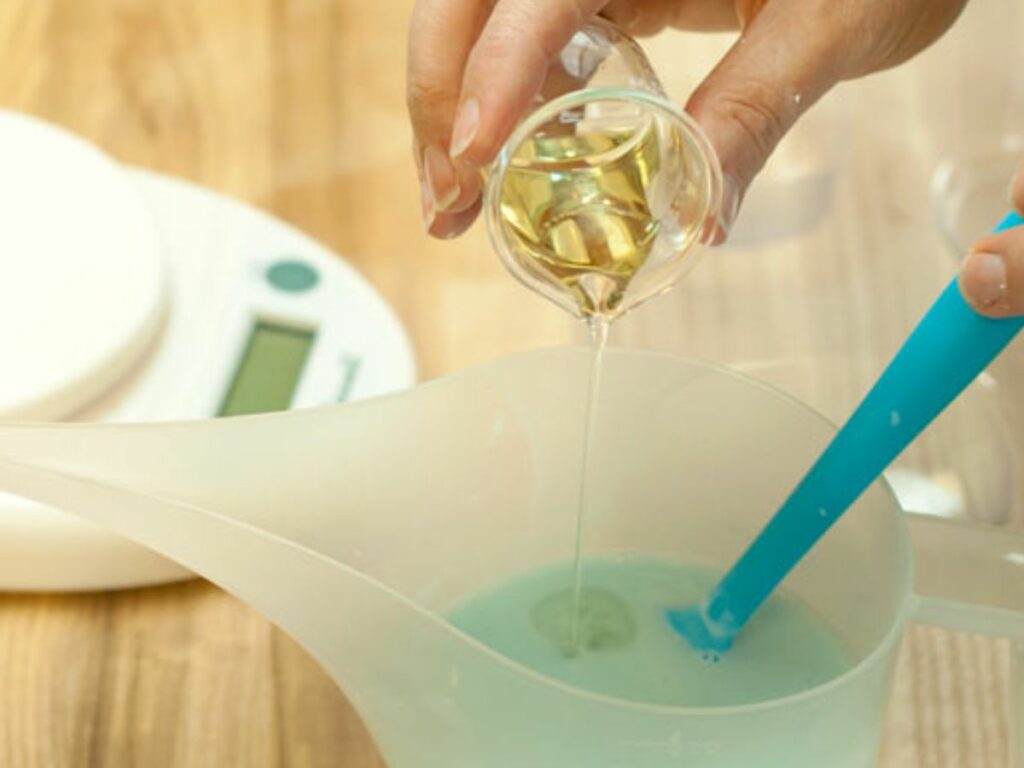
- Choosing Suitable Fragrances: Fragrances are added once the soap has cooled down to a certain temperature after the purification process. The precise temperature for addition varies based on the type of fragrance used but is generally kept low to preserve the integrity of the scent.
- Picking Appropriate Colorants: Fragrances are carefully measured to ensure the right concentration. They are then slowly blended into the soap mixture, using gentle mixing techniques to prevent any degradation of the scent. This ensures even distribution of the fragrance throughout the entire batch of soap.
- Adding Fragrances at the Right Time: Colorants are usually added to the soap mixture before it fully solidifies. This allows for better dispersion of the color throughout the soap. If added too early, especially during high-temperature phases, the color can degrade; if added too late, it might not mix well.
- Mixing in Colorants Effectively: Once added, the colorant is stirred thoroughly to ensure uniform distribution, avoiding streaks or concentrated spots. For instance, slow folding methods may be used to integrate the colorant without altering the soap’s texture. This process is done carefully to maintain the soap’s texture and consistency.
Step #5: Solidification and Drying
In the laundry soap manufacturing process, solidification and drying are pivotal stages that transform the soap from a liquid or semi-liquid state into a solid, usable form. Here are the key steps involved in this process:
- Gradual Reduction in Temperature: After the addition of fragrances and colorants, the next crucial step is to cool the soap mixture gradually. This controlled reduction in temperature is vital to ensure that the soap solidifies evenly, without forming cracks or inconsistencies.
- Monitoring the Consistency: Throughout the cooling process, the consistency of the soap is closely monitored. The goal is to achieve a uniform texture that is neither too hard nor too soft for the subsequent stages of milling and extrusion.
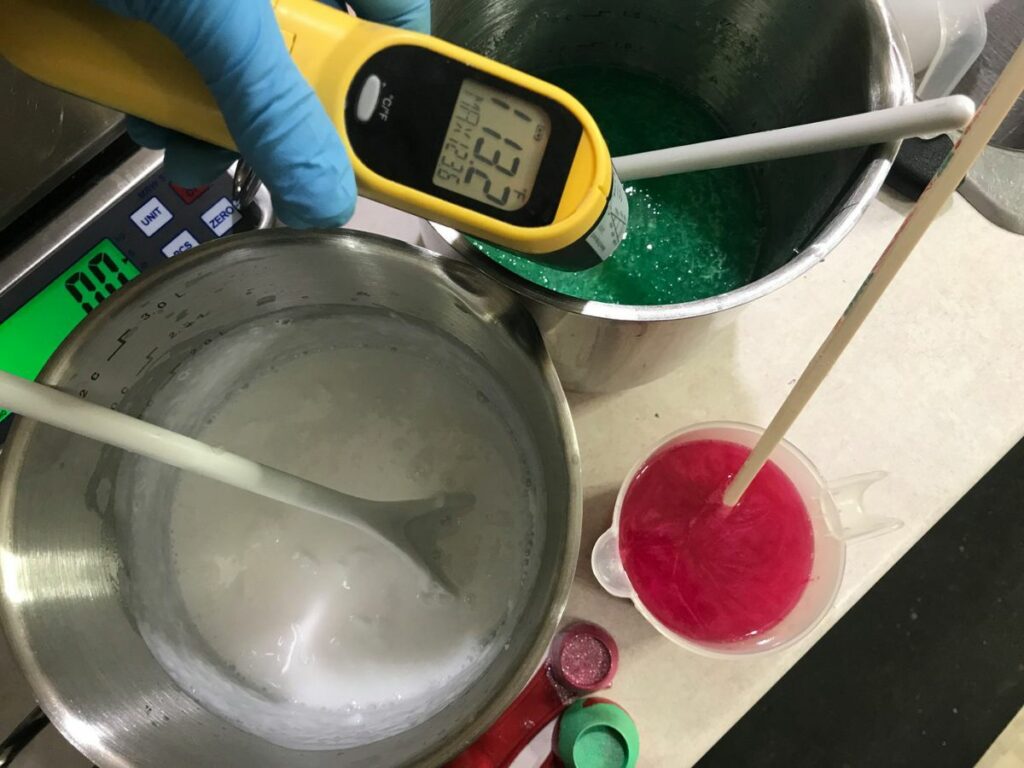
- Air Drying or Mechanical Drying: Once the soap has reached the desired consistency, it undergoes a drying process. This can be achieved through natural air drying or using mechanical drying equipment. The choice of drying method depends on the production scale and the specific requirements of the soap formulation.
- Maintaining Optimal Humidity Levels: The drying process is carefully controlled to maintain optimal humidity levels. This is crucial to prevent the soap from becoming too dry and brittle, which can affect its quality and performance.
Step #6: Milling and Plodding
In the sixth step of laundry soap manufacturing, we focus on the milling and plodding processes. Here are the details of these processes:
- Feeding Solid Soap into the Mill: According to Everything Supply Chain, the first step in milling is to feed the dried, solid soap into the mill. This is typically done using a conveyor system that transports the soap to the milling machine.
- Grinding to Achieve Fineness: In the mill, the soap passes through a series of rollers or blades that grind it into fine particles. The degree of fineness achieved in this process is crucial for the quality and texture of the final product.
- Continuous Monitoring and Adjusting: The soap’s texture is continuously monitored during milling, with adjustments made to maintain consistent particle size. For example, if the particles are too coarse, the speed of the rollers may be increased or the pressure applied to the soap may be adjusted.
- Transferring Milled Soap to the Plodder: After milling, the fine soap particles are transferred to a plodding machine. This machine is designed to compact the soap into a dense, homogenous mass.
Step #7: Extrusion and Cutting
The processes of extrusion and cutting are pivotal in shaping the final product. Here are the detailed steps involved in these processes:
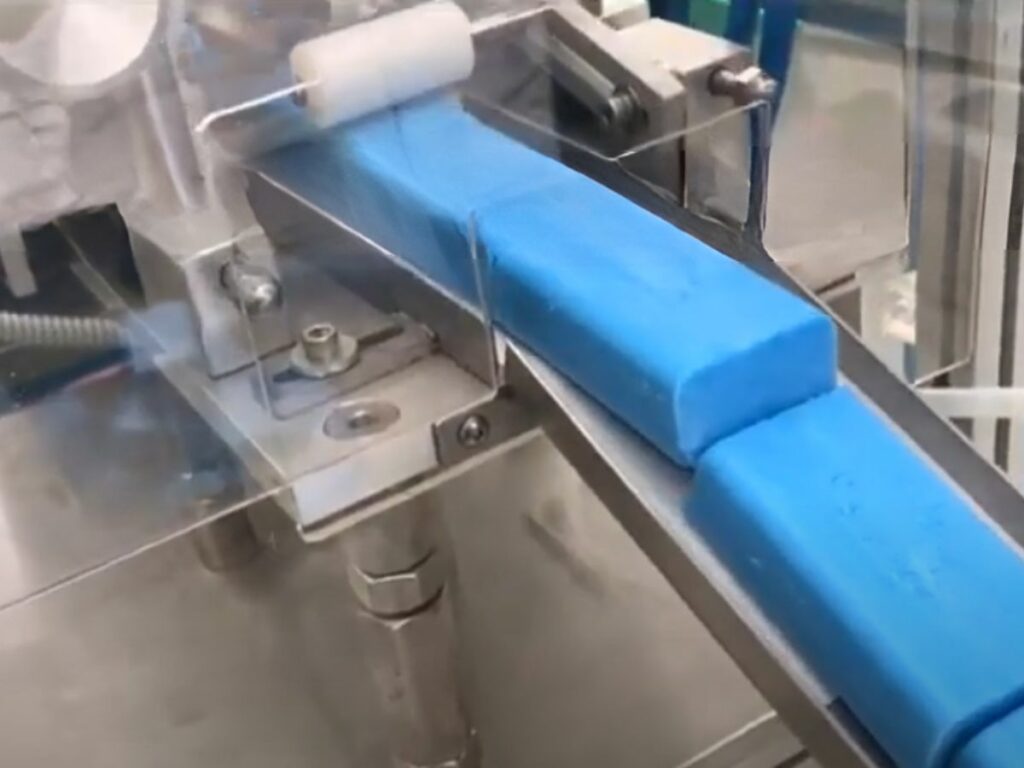
- Feeding Milled Soap into the Extruder: The extrusion process begins by feeding the milled and plodded soap into an extruder. The extruder is a machine designed to shape the soap into a continuous, uniform strand or bar.
- Applying Pressure for Consistent Shape: Inside the extruder, the soap is subjected to high pressure, pushing it through a die that shapes it into the desired form, typically a long, continuous bar. The pressure must be consistent to ensure uniformity in the soap’s density and dimensions.
- Controlling Temperature: The temperature within the extruder is carefully controlled. The right temperature is crucial for ensuring that the soap maintains its consistency without melting or becoming too hard, which could affect the extrusion process.
- Cutting the Extruded Soap into Bars: Once the soap is extruded into long bars, it is immediately cut into individual bars or pieces. This is done using a cutter, which can be either a wire cutter for softer soaps or a blade for harder varieties.
- Immediate Transfer to Further Processing: After cutting, the soap bars are immediately transferred to the next stages of production, which may include stamping, branding, or additional quality checks.
Step #8: Stamping and Branding
In the eighth step of laundry soap manufacturing, the stamping and branding process plays a crucial role in giving the soap its unique brand identity. Here’s a detailed look at the stamping process:
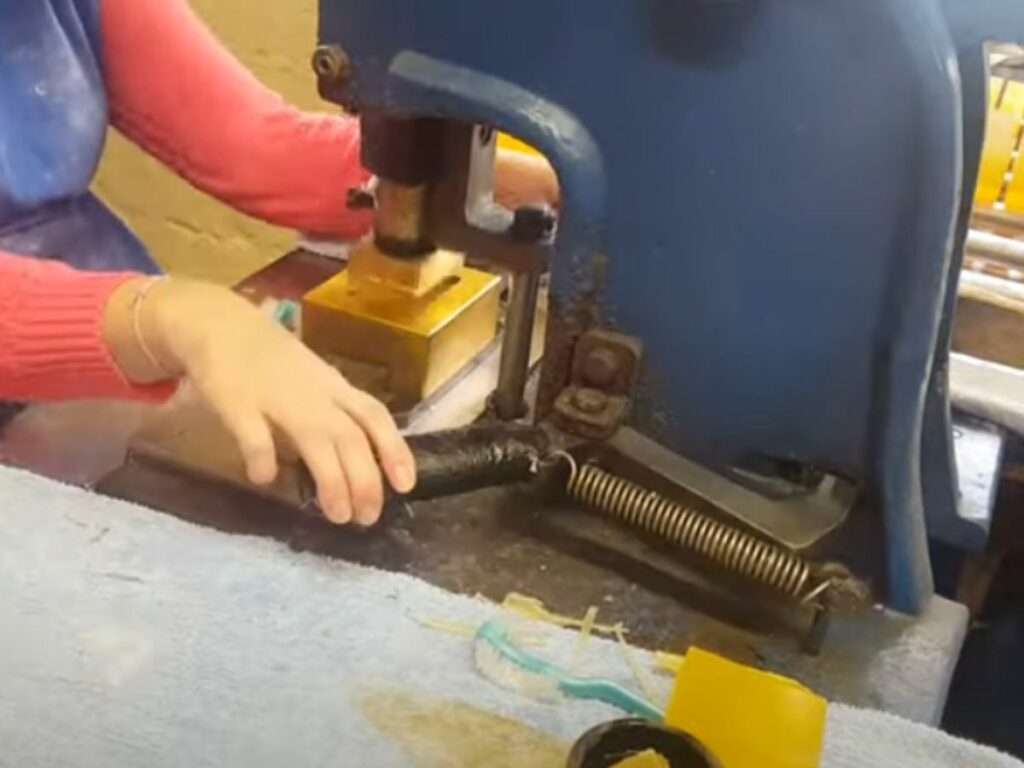
- Preparing the Stamping Equipment: Initially, the stamping equipment, including dies or molds with the brand’s logo or design, is set up. This equipment is specifically designed to accommodate the size and shape of the soap bars.
- Heating the Stamp: Depending on the type of soap and the desired effect, the stamp may be heated to a specific temperature. This is particularly important for soaps with a harder consistency, where a heated stamp ensures a cleaner and more precise imprint.
- Positioning the Soap Bars: The soap bars are aligned under the stamping machine. This alignment is critical and is often automated to ensure each bar is positioned correctly for a consistent imprint.
- Applying Pressure for Imprinting: The stamp is pressed onto the surface of the soap bar with precise pressure. This pressure is carefully calibrated to ensure the branding is deeply imprinted to last but not so deep that it deforms the bar.
Step #9: Quality Control and Testing
The focus in this step is on ensuring that each bar of soap meets the industry’s high standards for quality and safety. Here’s how the process of quality control and testing is typically carried out:
- Conducting Thorough Visual Checks: The process begins by mixing fats or oils with a strong alkali, typically sodium hydroxide (NaOH) for solid soaps or potassium hydroxide (KOH) for liquid soaps. The alkali is carefully measured to ensure the correct ratio for the saponification process, a technique meticulously followed by manufacturers like TY Cosmetic.
- Laboratory Testing for Composition and Performance: Samples from each batch are then sent to a laboratory for detailed analysis. These tests confirm the chemical composition of the soap, ensuring it matches the desired formula and is free from harmful contaminants.
- Durability and Safety Evaluation: The soap undergoes tests for durability, including shelf-life stability under various environmental conditions, to ensure it maintains its quality over time. Simultaneously, safety tests, particularly for skin sensitivity, are conducted to guarantee the product is hypoallergenic and safe for use.
- Approval and Record-Keeping: Following successful testing, the batch is approved for sale. Comprehensive records of the testing process, results, and any corrective actions taken are meticulously documented.
Consideration | Explanation |
Regulatory Compliance | Ensure adherence to local and national regulations governing soap manufacturing, including ingredient safety and labeling requirements. |
Production Documentation | Maintain comprehensive records of production processes, including batch records, quality control checks, and equipment maintenance logs. |
Ingredient Documentation | Keep detailed records of all ingredients used, including certificates of analysis, to demonstrate quality and traceability. |
Quality Control Approvals | Obtain internal and external approvals at various production stages to verify product quality and safety. |
Labeling and Packaging Compliance | Verify that soap packaging and labeling meet legal requirements, including ingredient lists, usage instructions, and safety warnings. |
Step #10: Packaging and Storage
The packaging and storage process plays a vital role in ensuring that the soap reaches the consumer in the best possible condition. Here’s a step-by-step overview of this process:
- Final Inspection and Alignment for Packaging: After passing quality control, the soap bars undergo a final inspection to ensure they are free of defects. They are then aligned and organized systematically for the packaging process, ensuring that each bar is ready for wrapping.
- Choosing and Utilizing Packaging Materials: The appropriate packaging materials are selected based on factors like brand image, market requirements, and environmental considerations. Options typically include paper wrappers, cardboard boxes, or plastic films. These materials are designed to protect the soap and maintain its quality during transit and storage.
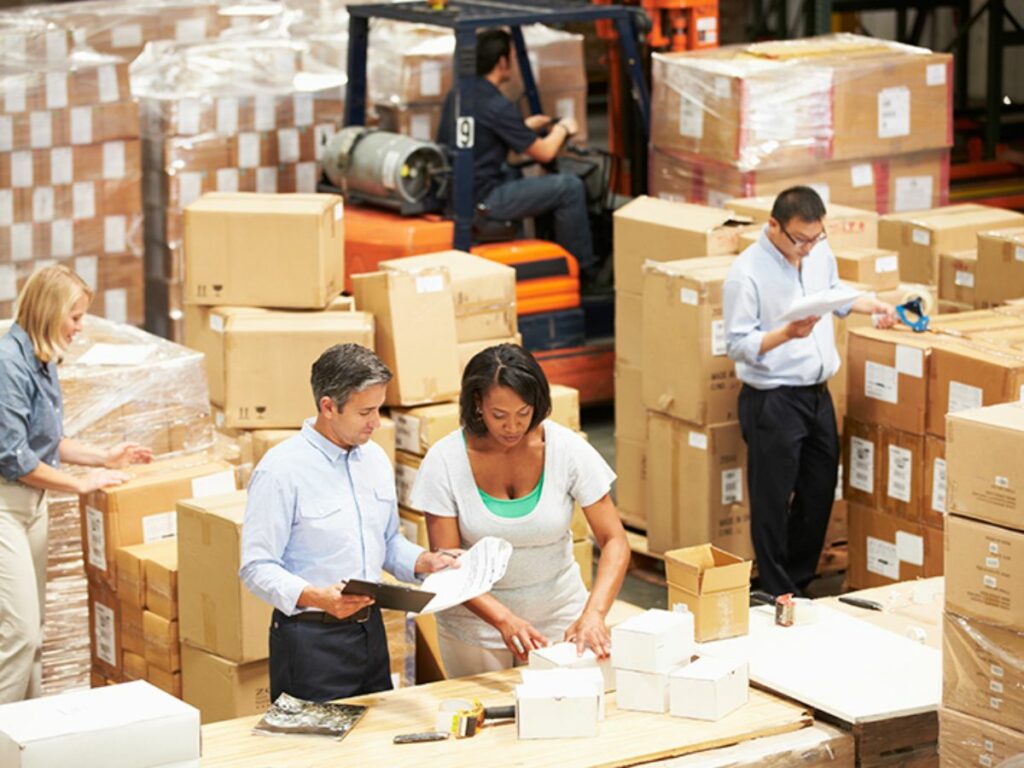
- Wrapping and Sealing the Soap Bars: The soap bars are then wrapped, either manually or via an automated process. Automated systems are efficient for large-scale production, wrapping and sealing the bars at high speed. Manual wrapping is often reserved for artisanal or specially shaped soaps, where a personal touch is required.
- Labeling, Coding, and Storage: Once wrapped, labels containing essential product information, such as ingredients, brand name, and usage instructions, are applied. Batch codes for traceability are also added. The packaged soaps are then carefully stored in a warehouse, under conditions that preserve their quality until they are shipped to retailers or directly to consumers.
Dive Deeper Into Our Resources
Interested in discovering more? Gain instant access to our diverse range of products:
Still haven’t found what you’re looking for? Don’t hesitate to contact us. We’re available around the clock to assist you
Conclusion
The journey through the 10 steps of laundry soap manufacturing reveals the complexity and precision that goes into creating a simple yet essential household product. This guide highlights the importance of each step in ensuring the quality and efficacy of the final product.
If you find this guide insightful and are looking to collaborate for your startup business, TY Cosmetic is here to assist. Contact us today for innovative solutions and expert advice in cosmetics manufacturing.